Magnetic Particle Inspection of Odd Shaped Parts
Numerous components in the automotive and engineering industry possess shapes that pose challenges for testing using conventional magnetic particle inspection machines. These parts are not easily loaded onto standard magnetic particle test benches and deviate from the current requirements specified in ASTM standards.
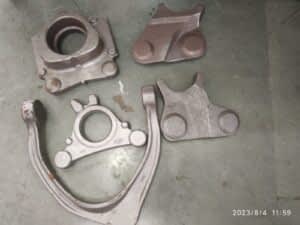
For these components, magnetization in two directions perpendicular to each other is essential. To address this requirement, a double-head machine has been developed, featuring two pairs of head and tailstocks perpendicular to each other for magnetizing the part.
The fields generated by both pairs are circular, yet perpendicular to each other. The calculation of the headshot current adheres to the ASTM standards formula:
Head Shot Current = 20 X Diameter (in mm)
Here, the diameter is determined as the maximum distance between any two points along the length of the part.
A tailor-made bench-type machine is employed for magnetic particle testing on these parts. Specially designed fixtures are used to position the part on the machine, and a pneumatically operated arrangement clamps the part from all four ends. This pneumatic clamping mechanism is crucial to prevent sparking when a high current is passed through the part. Additionally, the use of braided copper pads is recommended to eliminate arcing sparks, ensuring a safe and effective testing process.
Multidirectional magnetization is a specialized technique employed to identify defects in all orientations within a single examination. This differs from the combined magnetization shot used in traditional machines, which doesn’t adhere to ASTM standards. This technique is effective in identifying both longitudinal and transverse cracks in a single examination.
In this machine, multidirectional magnetization is used to detect defects in all directions in one shot.
Testing Procedure for Conventional Machines- Clean and dry the part’s surface before inspection.
- Place the part on the fixture.
- Apply a magnetic solution bath to the part.
- Press the ‘Cycle Start’ button.
- The part automatically gets clamped from all sides.
- Stop the flow of the bath.
- Now, the current passes through the part in multidirectional mode.
- Readings appear on the digital metering unit.
- The part automatically gets de-clamped.
- Inspect the front surface of the part under UV light for all defects.
- Remove the part and place it on the grills.
- Inspect the back surface of the part under UV light for all defects.
- Demagnetize