Case studies
Explore Our Impactful Case Studies. Witness the transformative power of our non-destructive testing and DFA solutions across industries. Discover how we've overcome challenges, optimized processes, and delivered exceptional results. Our real-world examples showcase our innovative approach and expertise. Unleash possibilities for your business by exploring our case studies today.
Case-Study #1
Problem Description:
Coincidently an operator observed a soft spot on a Steering Rack
Root cause was a water droplet from the cooling unit, occassionaly released during handling
40.000 units at risk, partly already at final assembly line in China, Germany, US
Client would not be able to manufacture replacement due to capacity constraints and lead time
40 DFA test devices were configured in 2 days, training of overseas operator included. 1 week the new procedure was qualified
100% inspection: 9 defective parts in 3 different batches found
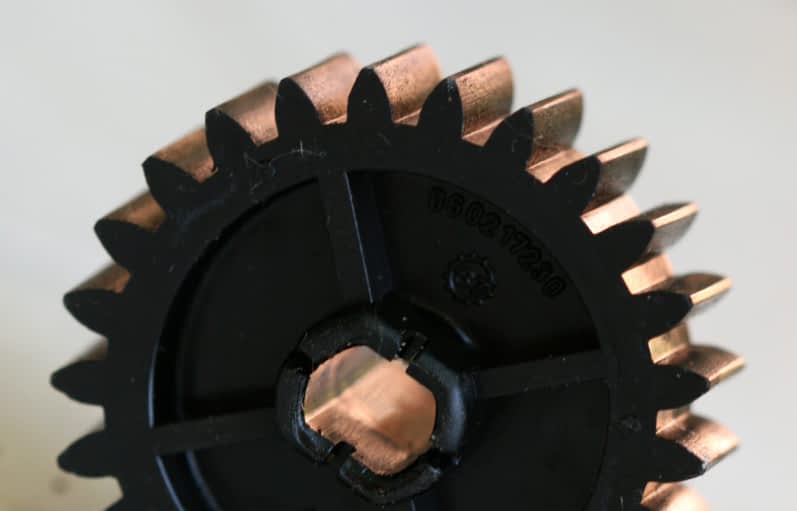
Client Name:
<confidential>
Current Status:
- DFA inspection added to standard IPC.
- Integration into lab machine started, 1st machine in use
Case-Study #2
Problem Description:
Mix-up of hardened / non-hardened products occured
Products shipped already to warehouse in Poland
Task was to sort hardened from non-hardened
Device was set up on site within 5 minutes
Inspection of 3.000 pieces within 6 hrs
Inspection speed faster than part handling for un-packing / packing
Client Name:
<confidential>
Current Status:
- Problem solved
- Huge saving for Roop and Its partner in Poland
Case-Study #3
Problem Description:
Two Wheeler Camshaft was reported in Japan for Low Hardness issue.
Interestingly, low hardness was observed in only Exhaust camshaft, Intake Camshaft was OK.
Mahle Camshafts Pvt. Ltd.
Client Name:
<confidential>
Current Status:
- DFA added to MIS-P.